記事公開日
最終更新日
金属溶射の選び方とは?導入前に知っておきたい5つのポイント
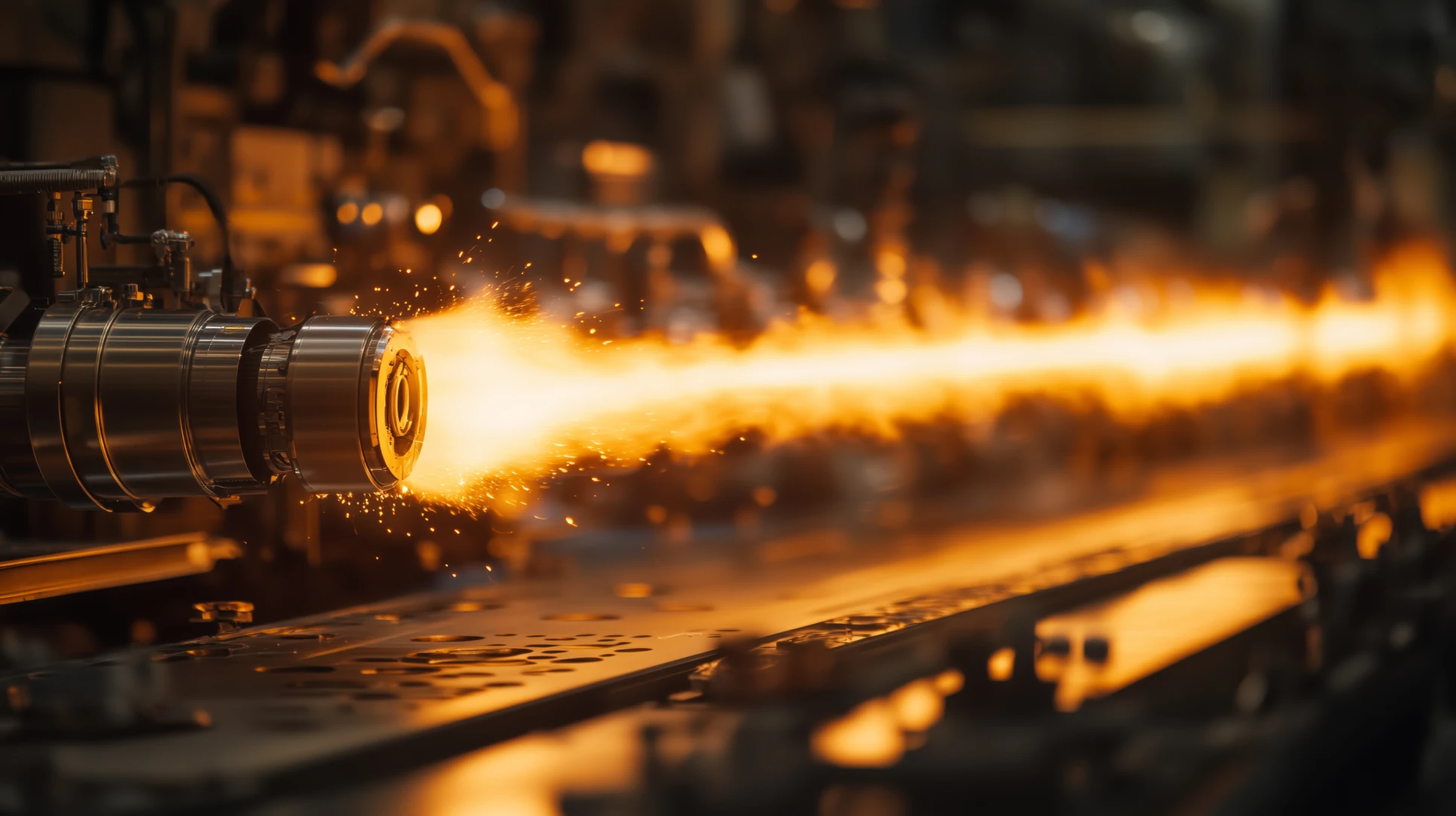
金属溶射は、橋梁や構造物、産業機械などの表面処理において、長寿命化・耐食性の向上を実現する重要な技術です。
しかし、「どの金属溶射方法を選ぶべきか」「溶射材の違いは?」「施工業者の選び方は?」といった疑問を持つ企業や公共団体の担当者は少なくありません。
この記事では、金属溶射の基礎知識をはじめ、選定時に注目すべき5つのポイントを具体的に解説いたします。
金属溶射とは?
金属溶射とは、金属の粒子を高温で溶融し、圧縮空気などで吹き付けることで、対象物の表面に金属皮膜を形成する技術です。
この皮膜は、耐食性・耐摩耗性・耐熱性といった特性を持ち、母材の長寿命化や性能向上に貢献します。
表面処理の一種として、橋梁やプラント設備、鉄塔、港湾構造物、さらには航空宇宙・自動車産業など、多様な分野で活用されています。
特に、過酷な環境にさらされる構造物においては、腐食防止対策が不可欠です。
金属溶射は、従来の塗装に比べて耐久年数が長く、メンテナンスの頻度やコストを大幅に削減できることから、インフラの維持管理における有力な手段とされています。
また、金属溶射は母材に大きな熱影響を与えず施工できるため、薄板や熱に弱い素材にも適用可能であり、修繕用途にも有効です。
最近では、耐久性能に加え、環境負荷の低減やSDGsに配慮した持続可能な管理手法としても注目されています。
このように、金属溶射はその多様な適用性と機能性から、現代のものづくり・社会インフラに欠かせない技術の一つとなっています。
金属溶射の種類とそれぞれの特徴
金属溶射にはいくつかの施工方式があり、それぞれ使用するエネルギー源や適用対象、形成される皮膜の特性に違いがあります。
用途や目的に応じて最適な方式を選ぶことで、より高い防食効果とコストパフォーマンスを得ることができます。
代表的な3方式の比較
アーク溶射
アーク溶射は、2本の金属ワイヤーを電気アークによって溶融し、圧縮空気で霧状にして対象物に吹き付ける方式です。
エネルギー効率が高く、施工速度も速いため、コストパフォーマンスに優れています。
主に鉄鋼構造物や橋梁、プラント設備の防錆処理に使われることが多く、量産・大面積の施工に向いています。
フレーム溶射
フレーム(炎)溶射は、ガス燃焼による熱で金属材料を加熱・溶融し、圧縮空気とともに吹き付ける方式です。
アーク溶射に比べるとやや手作業的で、制御が難しい面もありますが、低温処理が可能なため熱に弱い素材への適用に適しています。
小規模な補修や、複雑な形状の対象物に対応できるのも特徴です。
プラズマ溶射
プラズマ溶射は、プラズマアークを用いて極めて高温(1万℃以上)にしたガスで粉末状の金属やセラミックを溶融し、吹き付ける方式です。
非常に緻密で高硬度な皮膜が得られるため、耐摩耗性・耐熱性が求められる分野に適しています。
航空宇宙部品や高温部品への使用が多く、コストは高めですが、性能重視の場面では最適な手段です。
用途に応じた溶射材料の選び方
鉄、アルミニウム、亜鉛、セラミックスなど
金属溶射で使用される材料も、目的に応じて適切なものを選ぶことが重要です。
たとえば、亜鉛やアルミニウムは電気化学的な保護性能(犠牲防食)に優れており、橋梁や港湾設備など海辺のインフラに適しています。
鉄やスチール系の材料は機械的強度が求められる場面で使われ、セラミックやサーメット系の材料は耐摩耗性・耐熱性を重視する設備や部品に用いられます。
選定に際しては、対象物の使用環境や期待耐用年数、メンテナンス周期などを総合的に判断することが重要です。
適切な方式と材料を組み合わせることで、施工後の性能差が大きく変わるため、施工業者との十分な協議が欠かせません。
金属溶射の選び方:導入前に押さえておきたい5つのポイント
金属溶射を効果的に導入するには、単に技術を知るだけでなく、自社のニーズや条件に合った方式・材料・施工体制を見極めることが重要です。
以下に、導入前に必ず確認すべき5つの選定ポイントをご紹介します。
1.使用環境に適した溶射方式の選定
施工対象が屋外か屋内か、または海辺・高温・化学薬品が飛散するような特殊な環境かによって、適した溶射方式は異なります。
たとえば、海岸部の橋梁には防食効果の高い亜鉛やアルミニウムを使ったアーク溶射がよく選ばれます。
逆に、高温部品には耐熱性に優れたプラズマ溶射が適しています。
環境ごとのリスクを正確に把握し、耐用年数を含めて方式を選びましょう。
2.対象物の材質・形状への適合性
施工対象の材質(鉄鋼、アルミ、ステンレス、プラスチックなど)や形状(平面、曲面、複雑構造)によっても、選択すべき溶射方式が変わってきます。
熱影響を避けたい場合にはフレーム溶射が適しており、微細部や精密機器への施工には高精度なプラズマ溶射が求められることもあります。
対象物の特性に合った方式・材料を選ばなければ、密着不良や早期剥離の原因になります。
3.耐久性・コストのバランス評価
溶射方式や材料によって施工コストと耐久年数が大きく異なります。
初期コストが安くても、メンテナンス頻度が高くなればトータルコストは増加します。
たとえば、一般的な塗装よりも溶射の初期費用は高いものの、再施工サイクルが10~20年と長期にわたるため、結果としてコスト効率が良いこともあります。
ライフサイクル全体を見通した判断が必要です。
4.業者の施工実績と技術力
施工業者の経験・実績も選定時の重要な判断材料です。
金属溶射は高度な専門技術を要するため、実績の豊富な業者を選ぶことで施工品質の確保につながります。
特に、橋梁・プラント設備・大型構造物などの分野においては、同様の現場実績があるかを確認しましょう。
施工事例や工程管理体制を事前にヒアリングすることも重要です。
アフターサポートと品質保証の有無
施工後の品質維持には、点検・補修・保証といったアフターサポート体制が不可欠です。
万が一のトラブルに対応できる体制が整っているか、皮膜の保証期間はどの程度かなどを確認しましょう。
また、JISやISOなどの品質基準を満たしているかも安心材料の一つです。
信頼できる業者は、事前に詳細な見積・工程表・保証内容を明示してくれることが多いです。
まとめ
金属溶射は、インフラや構造物、産業機械の寿命を延ばし、メンテナンスコストを抑える有効な表面処理技術です。
しかし、施工方式や溶射材の選定を誤れば、期待する効果が得られず、逆に費用対効果を損なうリスクもあります。
この記事でご紹介した以下の5つの選定ポイント
1.使用環境に適した溶射方式の選定
2.対象物の材質・形状への適合性
3.耐久性・コストのバランス評価
4.業者の施工実績と技術力
5.アフターサポートと品質保証の有無
これらを事前に確認することで、より精度の高い導入判断が可能となります。
金属溶射の導入は、単なる技術選定ではなく、設備・インフラの将来を見据えた投資判断です。
ぜひこの記事の内容を参考に、自社にとって最適な選択を行ってください。