記事公開日
特殊溶接とは?製造業における導入メリットを解説!
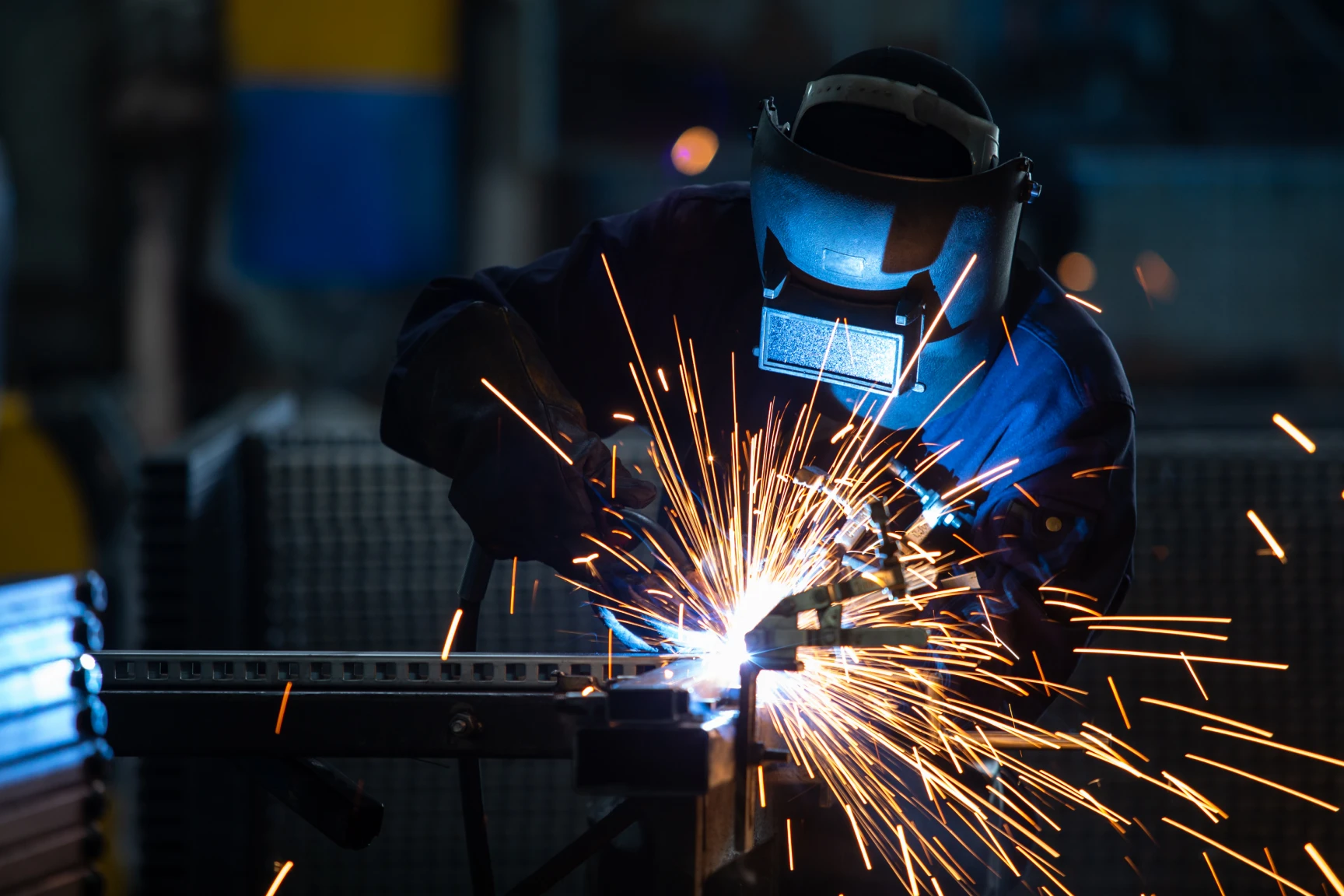
産業構造が高度化する中で、従来の汎用的な溶接技術では対応し切れない複雑な素材や加工ニーズが増加しています。
そんな中で注目を集めているのが「特殊溶接」です。
高精度・高耐久が求められる製造現場を中心に、従来工法にはない価値を提供するこの技術は、製造業の競争力向上に大きく貢献しています。
この記事では、「特殊溶接とは何か?」という基本から、導入のメリット、代表的な工法、活用事例、導入検討のポイントまで、網羅的にご紹介いたします。
特殊溶接とは?
一般的な溶接との違い
溶接とは、金属同士を高温で加熱して接合する加工技術のことを指します。
一般的に用いられるアーク溶接やガス溶接は、広く普及している標準的な工法ですが、これらは主に均一な素材や比較的単純な構造物に向いています。
一方で「特殊溶接」は、より複雑な条件に対応できる応用性の高い溶接技術です。
特殊溶接は、一般的な溶接が不得手とする異種金属の接合、微細部品の加工、極端な温度条件下での耐久性が求められる場面などで活躍します。
たとえば、粉体プラズマ溶接(PTA)や電子ビーム溶接などは、高精度かつ高強度な接合を実現でき、航空機部品や精密機械、自動車部品などの製造に欠かせない技術となっています。
特殊溶接が求められる背景
現在の製造業では、製品の多様化や軽量化、高性能化が進んでおり、それに伴って「通常の溶接では対応しきれない加工ニーズ」が増加しています。
たとえば、複雑な形状や厳しい耐摩耗性・耐熱性を求められる部品などは、従来の汎用溶接では十分な強度を確保できないことがあります。
加えて、リードタイムの短縮や品質の安定化、省エネ・環境配慮などの製造現場の要請に応えるためにも、より精度の高い溶接技術の導入が求められているのです。
こうした背景から、特殊溶接の技術は今後さらに重要性を増し、幅広い業界において導入が検討されるようになっています。
製造業の競争力強化を図る上でも、特殊溶接は有力な選択肢の一つといえるでしょう。
主な特殊溶接の種類
特殊溶接には多様な工法が存在し、それぞれが異なる目的や条件に適しています。
以下では、製造業で特に利用頻度が高く、応用範囲の広い主な溶接技術をご紹介します。
PTA溶接(粉体プラズマ溶接)
PTA(Plasma Transferred Arc)溶接は、粉末状の金属材料をプラズマアークによって溶融・被覆する高精度な表面処理技術です。
摩耗や腐食に強い層を形成することができ、バルブ、シャフト、ポンプ部品など耐久性が求められる部品に多く活用されています。
この工法の強みは、溶接の際に対象母材への熱影響が少ないため、寸法精度が保たれやすい点にあります。
特に精密機器や高機能部品の分野では、非常に有用な技術です。
TIG溶接
TIG(Tungsten Inert Gas)溶接は、タングステン電極とアルゴンなどの不活性ガスを用いたアーク溶接法です。
仕上がりの美しさと溶接品質の高さが特徴で、薄板や非鉄金属(アルミニウム、チタンなど)の加工に適しています。
特に食品加工設備や医療機器など、衛生性と精度が重要視される分野で多く用いられており、手作業による精密な制御が求められる点も特徴です。
被覆アーク溶接
被覆アーク溶接は、最も歴史のある溶接法の一つで、被覆材を持つ溶接棒を用いる手動式のアーク溶接です。
電源設備が簡易で持ち運びも容易なため、現場作業や補修作業で広く利用されています。
一方で、溶接品質は作業者の技術力に左右されやすく、自動化が難しいことから、大量生産よりも小ロット・多品種向けの工程で重宝されています。
複合技術(ロウ付・溶射・電子ビームなど)
近年では、複数の溶接・接合技術を組み合わせる「複合技術」のニーズも高まっています。
たとえば、ロウ付け(ろう付)や溶射、電子ビーム溶接などは、それぞれ特性が異なり、用途に応じて使い分けが可能です。
ロウ付けは比較的低温で接合でき、熱による素材の変形が少ないため、精密部品に適しています。
溶射は、金属粉末やセラミックを高速で吹き付けてコーティングを行うもので、耐摩耗・耐腐食性の向上に活用されます。
電子ビーム溶接は、真空中で高エネルギーの電子ビームを使って金属を溶融・接合する技術で、極めて精密な加工が可能です。
このように、複合技術は特殊溶接の可能性をさらに広げる手段として注目されており、製品品質の向上と設計自由度の拡大を実現します。
特殊溶接の導入メリット
特殊溶接は、従来の汎用的な溶接工法では実現が難しい品質や性能を提供することができるため、多くの製造業において導入のメリットがあります。
ここでは代表的な3つの利点を取り上げます。
耐久性・耐摩耗性を向上できる
特殊溶接は、高硬度・高耐久の金属素材を精密に溶着させることが可能なため、摩耗や腐食への耐性を大きく向上させることができます。
たとえば、PTA溶接によって形成される被覆層は、ポンプ部品や油圧シリンダーなど過酷な環境下で使用される部品に対して、長期間の使用に耐える性能を付与します。
このような耐久性の向上は、メンテナンス頻度の低減や部品交換サイクルの延長にもつながり、製造ラインの安定稼働に貢献します。
生産コストを削減できる
初期投資こそ一定のコストが必要となるものの、特殊溶接の導入により製品寿命が延び、保守・修繕にかかるランニングコストを削減することができます。
さらに、従来の部品交換を「修復・再利用」という方向にシフトすることで、コスト圧縮効果を生み出すケースもあります。
また、耐摩耗性の高い表面加工が可能になることで、低価格素材をベースに高性能部品を製造する「異材接合」戦略も実現可能となります。
製品寿命の延長と環境負荷の軽減を実現できる
高機能な溶接により製品寿命が延びることは、単にコストメリットを生むだけでなく、環境負荷の低減にもつながります。
たとえば、部品交換の頻度が減ることで廃棄物の削減が可能になり、資源の使用量を抑えることができます。
また、複合溶接技術によって機能性のある表面処理を施すことで、製品の再利用やリサイクル性が向上し、循環型社会の実現にも寄与する点は見逃せません。
まとめ
特殊溶接は、耐久性・精度・対応力に優れており、従来の溶接技術では実現できなかった加工を可能にします。
製造業における高度化・多様化するニーズに応える技術として、ますます注目が高まっています。
特に、高付加価値部品や厳しい耐久条件が求められる場面では、その導入効果は非常に大きいといえるでしょう。
これから特殊溶接の導入を検討される企業や団体にとっては、用途に最適な工法の選定や、信頼できる技術パートナーの存在が重要です。
特殊溶接は、単なる「接合技術」ではなく、製品品質やコスト競争力を根本から変える可能性を秘めた「経営資源」として、ぜひ積極的に活用をご検討ください。