記事公開日
溶射のメンテナンス方法とは?注意点やポイントを解説
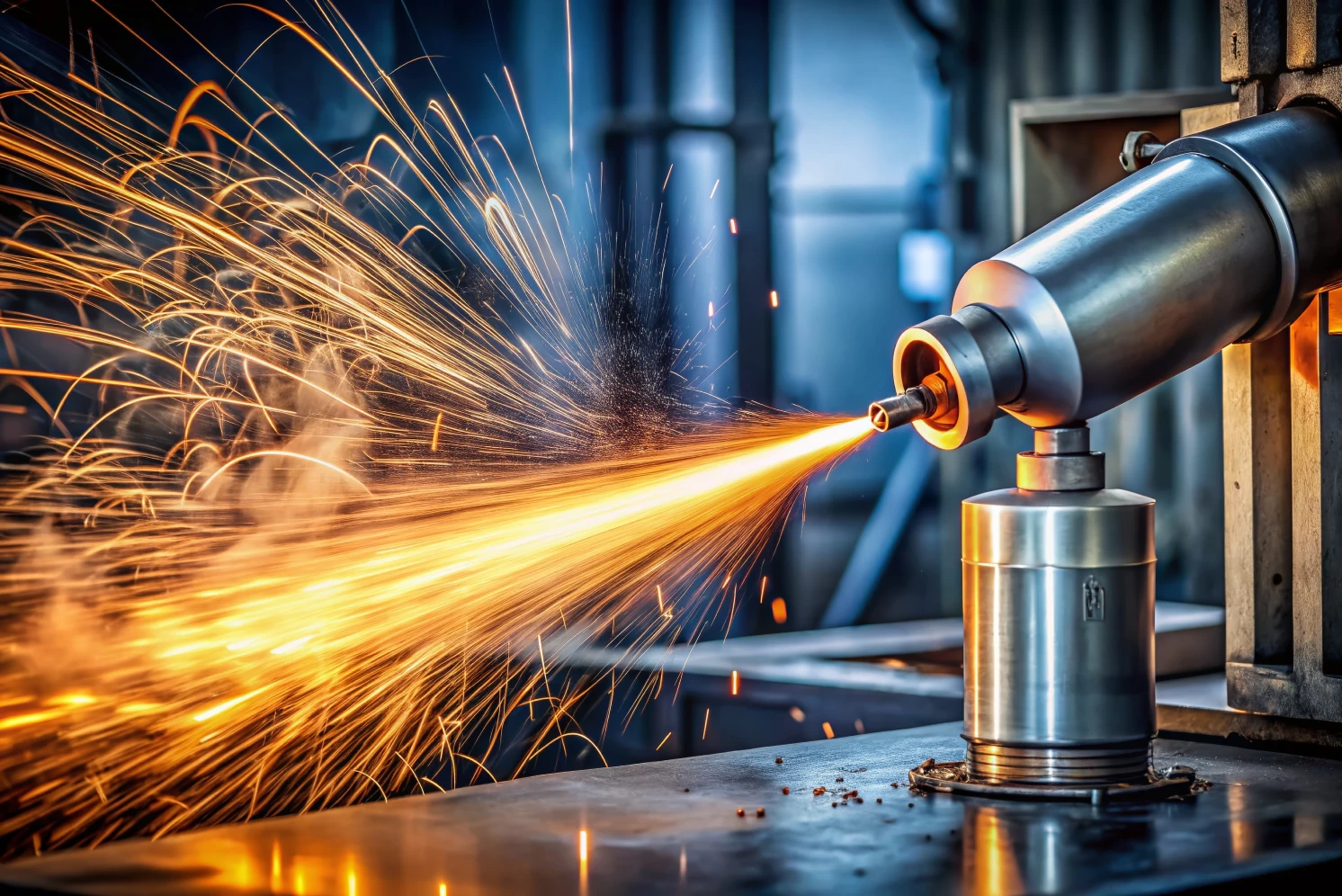
溶射技術は、金属やセラミックなどの材料を表面に吹き付けて機能性を向上させる加工方法で、摩耗や腐食への耐性強化に広く用いられています。
近年では、インフラ老朽化対策や産業設備の長寿命化ニーズの高まりから、溶射の活用が再注目されていますが、性能を維持するには適切なメンテナンスが不可欠です。
この記事では、溶射後のメンテナンス方法や注意点、管理ポイントについて、専門知識がなくても理解しやすいようにわかりやすく解説していきます。
溶射の一般的な工程
溶射処理は、表面改質の一手法としてさまざまな産業分野で利用されており、その効果を最大限に引き出すためには、工程ごとの確実な作業が欠かせません。
ここでは、溶射が実施される際の一般的な工程を、順を追って解説します。
工程1:対象物の洗浄
最初のステップは、溶射を施す対象物の洗浄です。
油分やほこり、酸化皮膜などが残っていると、コーティング材との密着性が著しく低下してしまいます。
通常は脱脂剤や有機溶剤、あるいはアルカリ洗浄を用いて、表面の不純物を除去します。
この工程は、後工程の品質を左右する非常に重要な前処理です。
工程2:粗面化処理(ブラスト)
洗浄後は、溶射材との接着性を高めるために「粗面化処理(サンドブラスト)」を行います。
これは金属ビーズやアルミナなどの研磨材を高速で吹き付けて、表面に微細な凹凸をつける処理です。
この凹凸がアンカー効果を生み出し、溶射皮膜の密着性を大幅に向上させます。
工程3:皮膜形成と溶射作業
次に、実際の溶射作業に入ります。金属やセラミック粉末を高温で加熱・溶融させ、対象物の表面に高速で吹き付けることで、機能性皮膜を形成します。
使用される溶射法には、ワイヤー溶射、プラズマ溶射、フレーム溶射などがあり、目的や素材に応じて選定されます。
この工程では、適切な温度・圧力・吹き付け速度の管理が非常に重要です。
工程4:熱処理と封孔処理
溶射後の皮膜は微細な空隙を含んでいるため、使用環境によっては酸化や腐食の原因になります。
これを防ぐために、熱処理による残留応力の除去と、シーリング材(封孔剤)を用いた封孔処理が行われます。
これにより、皮膜の耐久性と気密性がさらに高まり、長期使用にも耐えうる品質が確保されます。
工程5:仕上げ研磨と最終検査
最後に行われるのが、研磨と検査です。
溶射後の表面はやや粗くなっているため、機械的特性や寸法精度が要求される部品では、精密研磨が不可欠です。
鏡面仕上げが必要なケースでは、ラッピングやバフ研磨などの高精度加工も行われます。
研磨後は、外観検査・密着試験・硬度試験などの品質検査を実施し、製品としての信頼性を確認します。
溶射後に必要なメンテナンス方法
溶射処理を施した部品や設備は、使用環境によっては摩耗や腐食が徐々に進行するため、定期的な点検と適切なメンテナンスが求められます。
ここでは、維持管理のための基本的な考え方と実践ポイントを解説します。
メンテナンスのタイミングと頻度
溶射皮膜の寿命は、使用条件や環境によって大きく異なります。
高温・多湿、あるいは強い摩耗や化学薬品が関わるような環境では、皮膜の劣化が早く進む傾向があります。
そのため、点検のタイミングは少なくとも年に1回、過酷な環境下では半年に1回以上の定期的なチェックが推奨されます。
また、異常音や振動、性能の低下が見られた場合には、使用中でも早急な確認が必要です。
点検時に確認すべき劣化サイン
点検時には、以下のような兆候に注意が必要です。
- 皮膜の剥離やひび割れ:表面に不規則な亀裂や浮き上がりが見られる場合、密着性が失われている可能性があります。
- 摩耗や擦り減り:繰り返し接触する部品では、皮膜の厚さが減少していないかを確認します。
- 変色やサビの発生:封孔処理が不十分である場合、皮膜下で酸化が進行することがあります。
これらの劣化サインを見逃さず、早期に対応することで、部品の寿命延長や重大な故障の回避が可能となります。
部分補修と再施工の判断基準
点検の結果、劣化が局所的である場合は部分的な補修で済むケースも多く見られます。
たとえば、局部摩耗や小規模な剥離であれば、対象箇所を再研磨した後、再溶射による補修が可能です。
一方で、以下のような状況では全面再施工を検討する必要があります。
- 広範囲にわたる皮膜の損傷や剥離
- 基材(金属母材)へのダメージが進行している
- 使用性能が著しく低下している
再施工にはコストと時間がかかるため、事前の点検による早期発見・対応が極めて重要です。
メンテナンス時の注意点とポイント
溶射処理後のメンテナンスを適切に行うことで、部品や設備の寿命を大きく延ばすことが可能です。
しかし、方法を誤ると、かえって性能の低下や安全性のリスクにつながるおそれもあります。
以下では、注意すべきポイントと、安全性・信頼性を確保するための実践的な対策を紹介します。
誤った補修が招くトラブル
メンテナンス時に見落としがちなトラブルの代表例として、「誤った溶射材料の選定」や「適切でない下地処理」が挙げられます。
たとえば、腐食環境に適さない材料を使った補修を行うと、数ヵ月で再劣化が発生することがあります。
また、部分補修時に粗面化処理を十分に行わないまま再溶射すると、密着不良が生じ、皮膜がすぐに剥がれる事態に。
こうした不具合は、溶射本来の性能を発揮できないだけでなく、事故や設備停止などの重大な問題を引き起こす可能性があります。
安全性・信頼性を確保する対策
メンテナンスの品質を高めるには、次のような基本対策を徹底することが重要です。
- 事前調査の実施:使用環境、摩耗の進行度、基材の状態などを現場で丁寧に確認。
- 適正な再施工手順の遵守:洗浄・粗面化・溶射・封孔処理などを省略せず確実に実施。
- 性能試験による確認:補修後の密着強度や硬度を測定し、基準を満たしているかをチェック。
これらの対策を講じることで、溶射皮膜の安定性と耐久性を確保し、信頼性の高い運用が実現します。
専門業者に依頼する際のチェックリスト
外部業者に溶射メンテナンスを依頼する場合は、以下のような項目を事前に確認すると安心です。
対応する溶射法(ワイヤー、プラズマなど)に精通しているか
- 補修対象の部材や素材に関する実績があるか
- 点検・分析・報告書などを提供してくれるか
- 封孔処理や仕上げ加工まで一貫して対応できるか
- JIS規格やISOなどの基準に沿った施工をしているか
特に、再溶射だけでなく、長期的なメンテナンス設計ができる業者を選ぶことが、設備全体の信頼性を高めるポイントです。
信頼できる専門業者のひとつとして、光栄テック株式会社 のように、溶射加工から研磨・検査までをトータルで担える企業が挙げられます。
まとめ
溶射処理は、部品や設備の耐久性を飛躍的に向上させる有効な技術ですが、その性能を長く維持するためには、適切な「メンテナンス方法」を理解し、実践することが不可欠です。
この記事では、溶射の一般的な工程から、定期的な点検のポイント、劣化のサイン、補修・再施工の判断基準、さらにはメンテナンス時の注意点や専門業者選びのチェックリストまで幅広くご紹介しました。
特に重要なのは、初期段階での劣化兆候の発見と、適切な処置の実施です。
これにより、大規模な再施工を避け、コストの最小化と設備稼働率の最大化が図れます。
もし、現場の溶射メンテナンスについて少しでも不安がある場合は、経験豊富な専門業者に相談するのが賢明です。
たとえば、光栄テック株式会社のように、溶射から研磨・封孔処理・品質検査まで一貫して対応可能なパートナーに依頼すれば、施工品質とアフターサポートの両面で安心できます。
今後の設備管理・補修計画の一環として、この記事の内容をぜひご活用ください。