記事公開日
溶射加工とは?日本国内企業が知っておくべき技術の全て
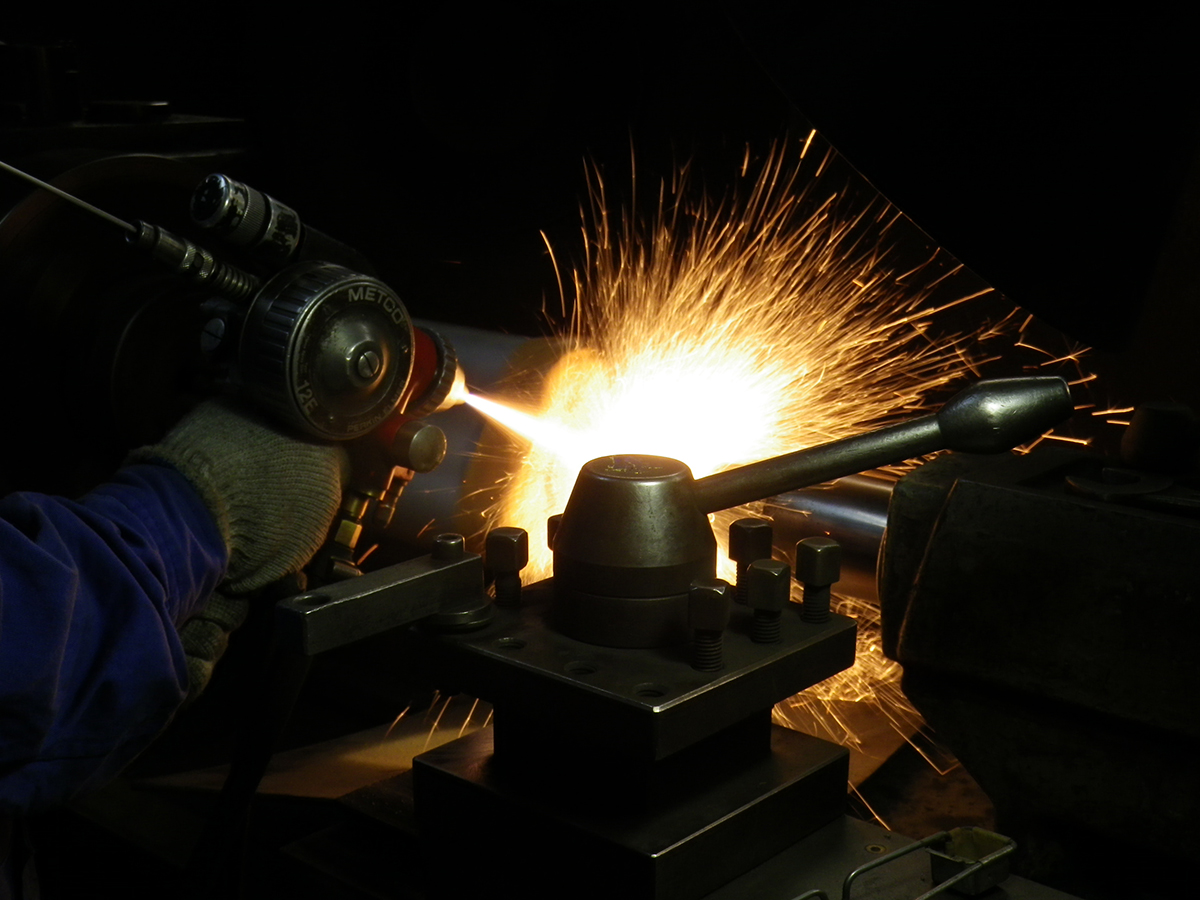
溶射とは、高温で溶かした材料を基材に吹き付ける技術です。
溶射加工は、耐摩耗性や耐食性の向上に役立ち、日本国内でも多くの企業で利用されています。特に製造業や建設業において、溶射加工の需要が高まっています。
この記事では、溶射加工の基本原理、種類、メリットとデメリット、そして実際の応用事例についてご紹介していきます。
溶射加工の基本原理
溶射のメカニズム
溶射加工とは、材料を高温で溶かし、それを基材に高速で吹き付けることによって表面を改質する技術です。このプロセスは、熱エネルギーを利用して材料を溶融し、それを高圧で噴射することで基材の表面に強固に付着させます。
熱エネルギーの利用
溶射加工では、ガス燃焼や電気アーク、プラズマなどの熱源を使用して材料を溶融します。
これにより、材料が基材の表面にしっかりと結合し、高い耐摩耗性や耐食性を実現します。
材料の溶融と吹き付け
溶融された材料は、高速で基材に吹き付けられます。この噴射プロセスにより、材料が基材に均一に付着し、滑らかで均一なコーティングが形成されます。噴射速度や圧力は、使用する材料や目的に応じて調整されます。
溶射加工の工程
溶射加工にはいくつかのステップがあり、それぞれが高品質なコーティングを実現するために重要です。
溶射準備
溶射加工の前には、基材の表面を清浄にするための準備が必要です。これには、サンドブラストや化学洗浄などの方法が用いられます。基材の表面が適切に準備されていないと、コーティングの付着性が低下する可能性があります。
実際の加工
基材の準備が整ったら、溶射プロセスが開始されます。溶射装置を使用して、溶融した材料を基材に吹き付けます。この工程では、高い精度と技術が求められます。
仕上げと検査
溶射加工が完了した後は、コーティングの品質を検査し、必要に応じて仕上げ作業を行います。コーティングの厚さや密着性を確認し、高品質な仕上がりを保証します。
溶射加工の種類
アーク溶射
アーク溶射は、電気アークを利用して材料を溶融し、圧縮空気で基材に吹き付ける方法です。
主に金属材料のコーティングに使用され、高い効率と経済性が特徴です。
アーク溶射のプロセスの詳細
アーク溶射では、2本の電極間にアーク放電を発生させて材料を溶融します。この溶融した材料を圧縮空気で基材に吹き付けることで、均一なコーティングが形成されます。
アーク溶射で利用される材料
アーク溶射には、鉄、アルミニウム、亜鉛などの金属材料が使用されます。これらの材料は、耐摩耗性や耐食性を向上させるために効果的です。
フレーム溶射
フレーム溶射は、ガス燃焼を利用して材料を溶融し、基材に吹き付ける方法です。耐熱性や耐食性が求められる用途に適しています。
フレーム溶射のプロセスの詳細
フレーム溶射では、ガスバーナーを使用して材料を溶融し、高速で基材に吹き付けます。溶融した材料は、基材の表面に均一に付着し、耐久性の高いコーティングを形成します。
フレーム溶射で利用される材料
フレーム溶射には、ニッケル、コバルト、タングステンなどの材料が使用されます。これらの材料は、高温環境や腐食性の高い環境での使用に適しています。
プラズマ溶射
プラズマ溶射は、プラズマアークを利用して非常に高温で材料を溶融し、高速で基材に吹き付ける方法です。高密度で非常に硬いコーティングを作ることができ、耐摩耗性や耐食性に優れています。
プラズマ溶射のプロセスの詳細
プラズマ溶射では、プラズマアークを発生させて材料を溶融し、高速で基材に吹き付けます。これにより、高品質で均一なコーティングが形成されます。
プラズマ溶射で利用される材料
プラズマ溶射には、セラミック材料や高融点金属材料が使用されます。これらの材料は、高性能部品や機器に適しており、耐摩耗性や耐熱性が求められる場合に効果的です。
HVOF溶射
HVOF(高速フレーム溶射)溶射は、非常に高い速度で材料を基材に吹き付ける方法です。これにより、非常に高密度で硬いコーティングが形成されます。
HVOF溶射のプロセスの詳細
HVOF溶射では、燃焼ガスを利用して材料を高速で基材に吹き付けます。このプロセスにより、非常に高い密度と強度を持つコーティングが形成されます。
HVOF溶射で利用される材料
HVOF溶射には、タングステンカーバイドやクロムカーバイドなどの硬質材料が使用されます。これらの材料は、特に耐摩耗性や耐食性が求められる用途に適しています。
溶射加工のメリット
耐摩耗性の向上
溶射加工によって基材の表面が硬化し、摩耗に対する耐性が大幅に向上します。これにより、機械部品や工具の寿命が延び、メンテナンスコストの削減につながります。
耐摩耗性の向上の例
例えば、ポンプのシャフトやインペラーに溶射コーティングを施すことで、摩耗による劣化を防ぎ、長期間にわたって高い性能を維持することができます。
耐食性の向上
溶射コーティングは、腐食に対する防護膜として機能します。特に、海洋環境や化学プラントなど、腐食性の高い環境下で使用される機器にとって、非常に有効な手段です。
耐食性の向上の例
海洋構造物やパイプラインに溶射コーティングを施すことで、塩害や化学腐食から基材を保護し、長期間の耐久性を確保します。
コスト削減
溶射は、初期投資が必要ですが、長期的にはメンテナンスコストの削減につながります。
長期的なメリット
溶射コーティングによって機械部品や構造物の寿命が延びるため、交換頻度が減少し、結果としてメンテナンスにかかるコストが削減されます。
溶射加工のデメリット
初期投資の高さ
溶射技術を導入するためには、専門的な装置や材料が必要となり、初期コストが高くなります。
導入コスト
溶射装置や熱源装置、材料などの導入には高額な費用がかかります。特に、中小企業にとっては大きな負担となることがあります。
技術的な難易度
溶射は高度な技術を必要とするため、専門知識と経験が求められます。
専門知識の必要性
溶射プロセスを正確に実施するためには、材料科学や熱処理技術に関する深い理解が必要です。これにより、適切なコーティングが施されることが保証されます。
まとめ
溶射加工は、さまざまな産業で重要な役割を果たしています。基材の表面特性を向上させ、長寿命化やコスト削減に寄与する一方で、高度な技術と初期コストが必要です。しかし、その多くのメリットを考慮すると、溶射技術は今後ますます重要となるでしょう。
以上で、溶射加工に関する基本的な原理と応用についての解説を終わります。興味を持たれた方は、さらに詳細な情報を専門の技術資料などでご確認ください。