記事公開日
溶射と溶接の違いとは?それぞれの特徴や用途を解説
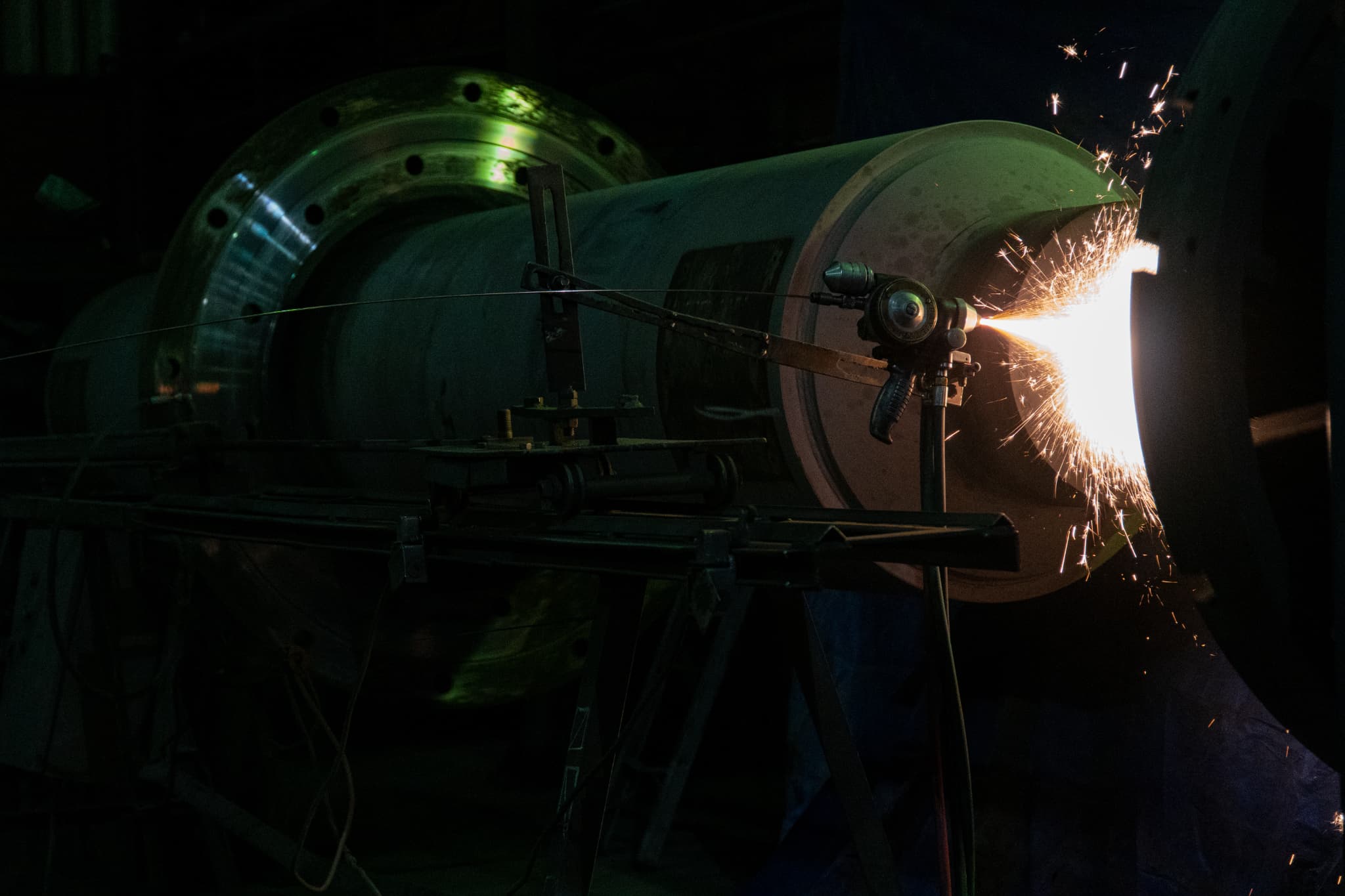
「溶射」と「溶接」は、どちらも素材や製品に特殊な加工を施す技術ですが、実際には用途や目的に大きな違いがあります。 溶射は主に表面処理に用いられ、耐久性や耐熱性の向上を目的とするのに対し、溶接は部品同士を一体化させる接合技術です。
耐久性を求めるインフラ整備や産業機械の分野で溶射技術が注目される一方、自動車や建設などの領域では強度の高い溶接技術が利用されています。
この記事では、溶射と溶接の違い、それぞれの特徴や用途についてご紹介いたします。
溶射とは?
溶射は、金属やセラミックなどの材料を微粒子にし、高温で溶融させて対象物の表面に吹き付け、コーティング層を形成する技術です。
溶射は、対象物の耐久性や耐食性、耐熱性を高めるために利用され、表面保護に特化した加工方法として、幅広い産業で活用されています。
特にインフラ設備や機械部品など、摩耗や腐食の影響を受けやすい部品に対して使用されることが多く、経済的にも効果的な表面処理技術として注目されています。
溶射の特徴
溶射には、以下のような特徴があります。
表面保護に優れている
溶射により形成されるコーティング層は、摩耗や腐食、熱に対する耐久性が向上します。
これにより、インフラや産業機械の部品寿命が延び、維持管理コストの削減につながります。
低温での加工が可能
溶射は高温で微粒子を吹き付ける一方、対象物自体は高温にしなくて良いため、熱変形が気になる部品にも対応可能です。
広範な材料に対応
金属、セラミック、カーボンなど、さまざまな素材が溶射のコーティング材として使用できます。
これにより、特定の用途に合わせたカスタマイズが容易に行えます。
溶射の活用例
溶射は、特にインフラや産業分野において以下のような用途で広く活用されています。
橋梁や水道管などのインフラ設備
耐久性が求められるインフラの保護コーティングとして溶射が利用されています。
表面が摩耗や腐食にさらされやすい橋梁や水道管に施すことで、長期間にわたり耐久性が保たれます。
発電プラントや石油化学プラントの設備
発電設備や化学プラント内の配管や機械部品にも溶射が施され、腐食や摩耗への耐久性が強化されます。
高温環境にさらされる部品にも適用可能なため、保守管理の頻度を下げ、長寿命化を実現します。
産業機械の部品
溶射により、切削工具やプレス機の部品の表面を強化し、摩耗による寿命短縮を防ぎます。
これにより、生産設備のダウンタイムを減らし、稼働効率を向上させる効果も得られます。
溶射については、下記の記事もご覧ください。
【関連記事】
溶射とは何か?基本原理から応用まで徹底解説
溶接とは?
溶接は、金属や合金などの部品を高温で加熱し、接合させる技術です。
溶接の目的は、複数の部品を一体化することで強度を高め、接合部が一つの材料として機能するようにすることです。
溶接は自動車や建設分野をはじめ、製造業やインフラ関連でも広く使用されており、部品同士の強力な接合が求められる場所で不可欠な加工技術です。
溶接の特徴
溶接には、以下のような特徴があります。
高い接合強度
溶接により、複数の部品を一体化することで、元の材料と同程度の強度を持つ接合が実現されます。
このため、衝撃や振動に強く、長期的な使用にも耐える構造が得られます。
多様な溶接方法
アーク溶接やガス溶接、レーザー溶接など、使用材料や用途に応じた溶接方法が多数存在します。
それぞれの方法には特有の利点があり、用途や環境に応じた最適な方法を選べることが特徴です。
熱影響による変形リスク
溶接では接合部を高温で加熱するため、熱による金属の変形や歪みが発生する可能性があります。
そのため、溶接後の冷却方法や補強処理が求められる場合もあります。
溶接の活用例
溶接は、多くの製造業やインフラ関連プロジェクトにおいて、以下のような場面で活用されています。
建設業界での鉄骨構造の接合
建設現場では、鉄骨を組み立てる際に溶接を用いて各部材を強固に接合します。
これにより、高い強度と安全性が求められるビルや橋梁などの構造物が作り上げられ、耐震性の確保にも寄与しています。
自動車製造における車体フレームの一体化
自動車の車体フレームやシャーシの製造では、溶接により複数のパーツを一体化し、剛性と耐久性を高めます。
これにより、走行時の衝撃に対する耐性や衝突時の安全性が向上します。
配管やタンクの製造
高圧に耐える必要がある配管やタンクの製造にも溶接が用いられます。
これにより、漏れのない強固な接合が実現され、石油やガスといった液体や気体を安全に運搬・保管することが可能になります。
溶射と溶接の用途別の使い分け方
溶射と溶接は、それぞれ異なる特性と目的を持つ加工技術であり、用途や状況に応じて使い分ける必要があります。
以下に、用途別に溶射と溶接の特性を活かした使い分け方を解説します。
インフラ設備や産業機械では「溶射」を多用
溶射は、耐久性や耐熱性が求められるインフラ設備や産業機械の部品に広く使用されます。
例えば、橋梁や水道管、発電プラントの設備など、腐食や摩耗の影響を受けやすい環境において、溶射は表面保護を目的としたコーティングとして効果を発揮します。
溶射によって表面の耐久性が高まるため、メンテナンス頻度が低減し、長期的なコスト削減にもつながります。
また、産業機械の部品にも適用され、摩耗しやすい部品の寿命を延ばすことで、生産ラインの効率維持に貢献しています。
建設業や自動車製造業では「溶接」を多用
一方、溶接は金属部品を強固に接合する必要がある建設業や自動車製造業で多く活用されています。
建設分野では、建物の骨組みや鉄骨の接合に用いられ、高い強度と安全性が求められる構造物を形成します。
自動車製造でも、シャーシやフレームなど、強度が要求される部位に対して溶接が施され、一体化による剛性の向上と衝撃吸収性が高められています。
これにより、耐久性が求められる大型設備や構造物において、溶接が欠かせない技術となっています。
コストパフォーマンスと耐久性を比較して使い分け
溶射と溶接は、それぞれコストと耐久性においても異なるメリットを持っています。 溶射は、表面にコーティングを施すため、全体の強度を高めるよりも表面保護が目的です。 そのため、特定の部分にだけ耐久性を持たせたい場合に有効で、比較的コストパフォーマンスに優れた方法です。
まとめ
溶射と溶接は、異なる目的と特性を持つ技術であり、それぞれに適した用途があります。溶射は、主に耐久性や耐食性、耐熱性を高めるための表面処理技術で、インフラや産業機械の部品保護に最適です。これにより、部品の長寿命化とメンテナンスコストの削減が期待できます。一方、溶接は、部品同士を強固に接合し、一体化を図る技術です。特に自動車や建設業のような高い強度が求められる分野で不可欠な役割を果たしています。
溶射と溶接のどちらを選ぶべきかは、製品や部品の用途、求められる耐久性やコストなど、さまざまな要素に依存します。例えば、部品表面の保護が目的であれば溶射が適しており、強度や耐久性のある接合が必要であれば溶接が適しています。
この記事で紹介したように、溶射と溶接はそれぞれ異なる利点と特徴を持つため、目的に応じた適切な技術を選ぶことが重要です。製造やメンテナンスの効率を最大限に高めるためにも、それぞれの技術の理解を深め、活用を検討してみてください。