記事公開日
溶射の用途には何がある?多分野での活用例と基本知識をご紹介
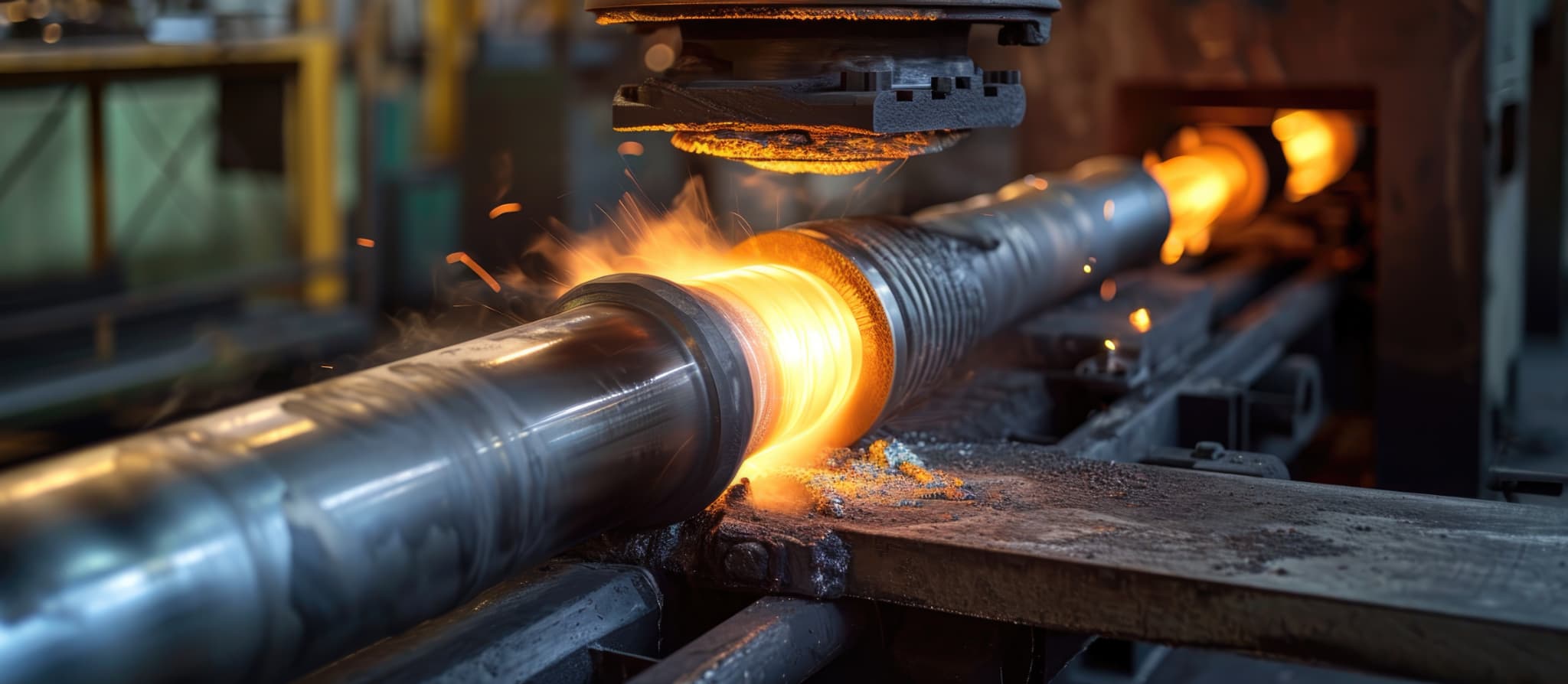
溶射は、金属やセラミックの粉末を高温で溶融し、製品の表面にコーティングする技術で、多様な分野で広く利用されています。
耐摩耗性や耐腐食性の向上はもちろん、断熱性や電気特性の付与など、その用途は非常に多岐にわたります。 日本国内でも、製造業からインフラ整備まで幅広い業種で採用されており、競争力を高めるための重要な技術とされています。
本記事では、溶射の基本的な用途から具体的な活用例までをわかりやすく解説します。
溶射とは?
溶射とは、金属やセラミックの粉末を高温で溶融し、製品の表面に吹き付けることでコーティングを施す技術です。
溶射によって、製品の耐摩耗性や耐腐食性が向上し、使用寿命が大幅に延びることが期待できます。
さらに、断熱性や電気特性の付与、表面の修復や寸法復元といった特殊な用途にも活用されています。
溶射の用途一覧
溶射技術は、その多様性からさまざまな業界で活用されています。
以下に、代表的な用途を詳しく解説します。
耐摩耗性向上:機械部品や工具の寿命延長
溶射技術は、摩耗の激しい機械部品や工具の表面を強化するために利用されます。 例えば、切削工具やポンプ部品などに溶射を施すことで、摩擦による劣化を抑え、耐久性を向上させます。 これにより、交換頻度を減らし、長期的なコスト削減が期待できます。
活用例:
- 自動車エンジン部品
- 工作機械の切削工具
耐腐食性向上:インフラや海洋構造物の保護
海水や化学物質にさらされる環境では、金属の腐食が重大な問題となります。 溶射は、インフラや海洋構造物の防錆対策として広く活用されています。鋼材の表面に耐腐食性の高い材料をコーティングすることで、腐食の進行を防ぎます。
活用例:
- 橋梁の鋼材
- 海洋プラットフォームの支柱
断熱・耐熱用途:航空機エンジンや産業用ボイラー
溶射技術は、高温環境での耐久性向上やエネルギー効率の改善にも寄与します。 航空機エンジンのタービンブレードや産業用ボイラーに使用することで、断熱性を強化し、性能を最大限に引き出します。
活用例:
- 航空機エンジンのタービンブレード
- 発電所のボイラー内壁
電気特性付与:電子部品やセンサー技術
溶射は、特定の電気特性を持つ表面を作り出すためにも利用されています。 センサーや電子部品に適用することで、導電性や絶縁性を付与することが可能です。
活用例:
- 半導体部品のコーティング
- 精密センサーの電極形成
表面修復・肉盛り:部品の寸法復元やリサイクル
摩耗や損傷により使用不能となった部品に溶射を施し、表面を修復する用途もあります。 肉盛り加工により、部品の寸法を復元し、再利用可能な状態に戻します。 これにより、部品のリサイクル率を向上させ、コスト削減と環境保護に寄与します。
活用例:
- 大型機械部品の表面修復
- 産業機械のリサイクル部品加工
溶射の活用例
溶射技術は、その多用途性から製造業や建設業、エネルギー分野など幅広い産業で活用されています。
以下では、それぞれの分野での具体的な活用例を紹介します。
製造業:自動車エンジン部品や工作機械
製造業では、溶射技術が特に重要な役割を果たしています。 自動車のエンジン部品では、摩耗や高温に耐える特性が求められます。 溶射を用いることで、部品の寿命を延ばし、エネルギー効率の向上を実現しています。 また、工作機械の部品にも溶射が施され、摩擦や腐食からの保護を提供しています。
具体例:
- エンジンのシリンダーライナー:耐摩耗性と熱効率の向上。
- 切削工具:表面強化による長寿命化と加工精度の向上。
建設業:橋梁やトンネルの保護コーティング
建設業では、溶射技術がインフラの長期的な耐久性向上に役立っています。 特に、橋梁やトンネルでは、鋼材を腐食や摩耗から守るために溶射が活用されています。 塩害や大気中の汚染物質による腐食を防ぎ、構造物の安全性と寿命を確保します。
具体例:
- 橋梁の鋼材コーティング:塩害や湿気による腐食防止。
- トンネル内壁:摩耗耐性を高めるための溶射コーティング。
エネルギー分野:発電タービンやパイプライン
エネルギー分野では、高温や高圧といった過酷な環境下で使用される設備に溶射が不可欠です。 発電所のタービンブレードには、断熱性や耐熱性を向上させるために溶射技術が採用されています。 また、石油やガスを輸送するパイプラインにも溶射が施され、腐食や摩耗を防ぎます。
具体例:
- 発電タービンブレード:高温環境での耐久性向上。
- 石油パイプライン:腐食防止と輸送効率の向上。
溶射技術を選ぶ際のポイント
溶射技術を導入する際には、製品やプロジェクトのニーズに応じて最適な選択をすることが重要です。
以下では、溶射技術を選ぶ際に考慮すべき主要なポイントを解説します。
使用する基材に適した溶射材料の選定
溶射技術は、適用される基材の種類や用途に応じて、使用する材料を適切に選定する必要があります。一般的に、溶射材料として使用されるのは以下のようなものです。
- 金属系材料:耐摩耗性や耐腐食性が求められる場合に適しています。
- セラミック系材料:断熱性や電気絶縁性を付与する用途で活用されます。
- ポリマー系材料:非粘着性や滑り性を必要とする場合に使用されます。
材料の選定は、基材との相性やコーティング後の性能に直接影響を与えるため、事前の試験や専門的なアドバイスを受けることが推奨されます。
導入コストと長期的な効果の比較
溶射技術の導入には初期コストがかかることが一般的です。 ただし、長期的な視点で見た場合、メンテナンスコストや部品の交換頻度を削減できるため、総合的なコスト削減につながる可能性があります。
比較のポイント:
- 短期コスト:導入に必要な設備費や施工費
- 長期効果:製品寿命の延長、メンテナンス回数の削減
導入コストが高いと感じても、長期的な効果を評価することで、溶射技術の採用が費用対効果の高い選択肢であることがわかるでしょう。
専門業者選びのチェックポイント
溶射技術の効果を最大化するためには、信頼できる専門業者を選ぶことが重要です。 以下の点に注目して業者を選定しましょう。
- 技術力と実績:過去の施工例や業界での経験年数を確認します。
- 対応可能な材料と基材:自社製品に適した溶射を提供できるか。
- アフターサポート:施工後のメンテナンスやトラブル対応が整備されているか。
選定時には、複数の業者から見積もりを取り、サービス内容やコストを比較することをおすすめします。
まとめ
溶射技術は、製品の性能向上や耐久性の向上、さらには環境負荷軽減にも寄与する重要な表面処理技術です。製造業や建設業、エネルギー分野など、さまざまな業界でその有用性が証明されています。
溶射技術を適切に活用することで、製品の性能向上やコスト削減が実現し、競争力を高めることができます。 導入を検討する際には、自社のニーズを明確にし、信頼できる専門業者と連携することが成功の鍵となります。
技術の進化により、溶射プロセスはより精密化し、幅広い用途での採用が期待されています。 また、持続可能な生産を実現するための重要な技術として、今後さらに注目されるでしょう。