記事公開日
溶射のメリットとは?なぜ今、溶射が注目されているのか?
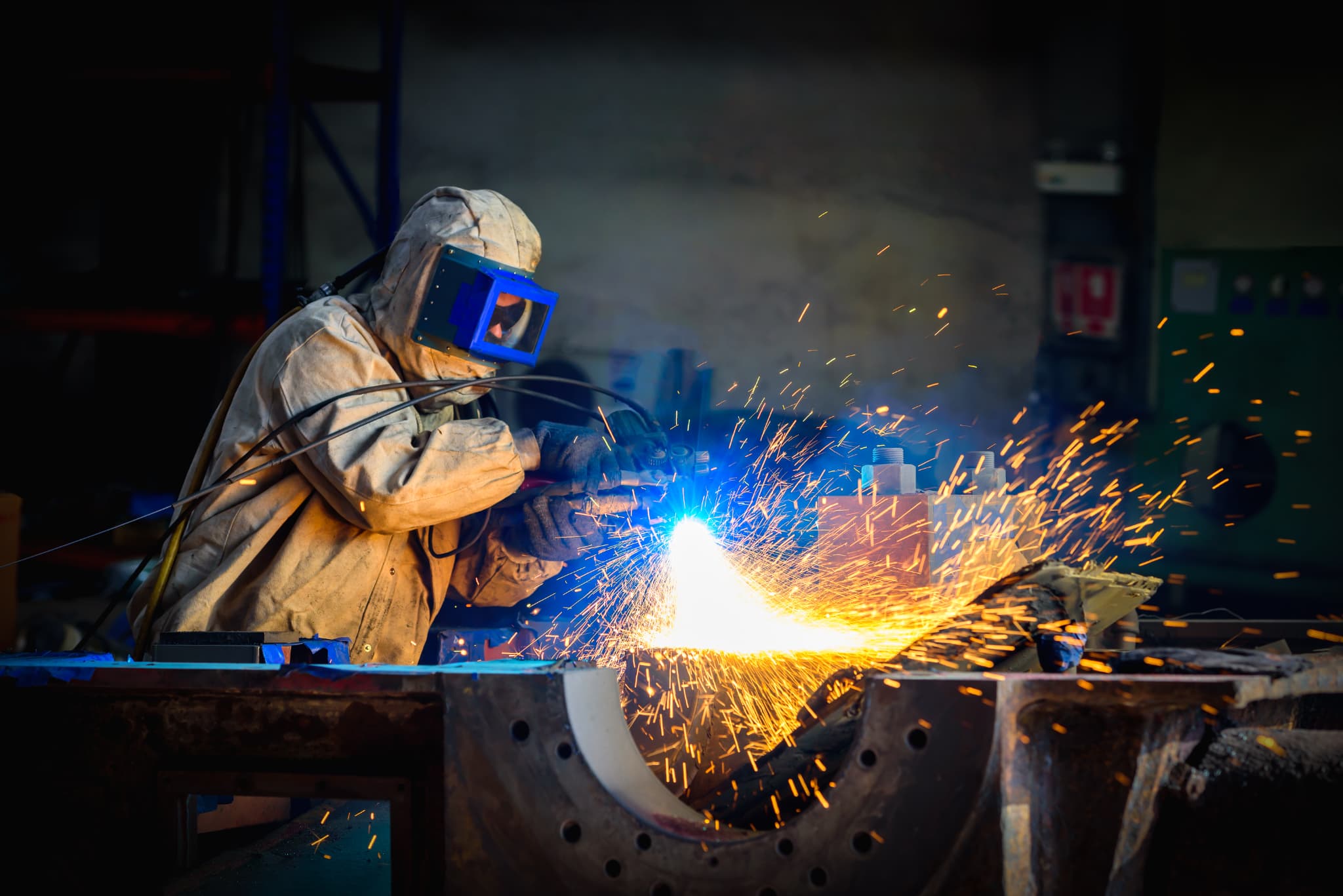
溶射とは、製品の表面に特定の材料をコーティングし、耐久性や耐摩耗性を向上させる技術です。
日本国内でも、製造業や公共インフラの分野でその活用が広がりつつあり、企業の生産性向上に重要な役割を果たしています。 特に、エネルギー効率や環境負荷軽減といった課題に対応できる点で注目されています。
本記事では、溶射の基本的な仕組みからメリット・デメリットまでを解説いたします。
溶射とは?
溶射とは、金属やセラミックなどの粉末状材料を高温で溶融し、製品表面に吹き付けることで、耐摩耗性や耐腐食性を向上させる技術です。
溶射は、自動車、航空、建設業界などの製造分野だけでなく、インフラ設備やエネルギー関連施設でも広く利用されています。
溶射の基本原理は、材料を加熱して溶融させ、その流体を高速で基材表面に吹き付けることで、強固なコーティング層を形成する仕組みです。これにより、基材自体の性質を保ちながら、耐久性や特定の機能を付加することが可能になります。
溶射が注目される背景
近年、企業の競争力向上や持続可能性への意識の高まりを背景に、溶射技術の需要が増加しています。特に、以下のような要因が挙げられます。
- 耐久性の向上:設備や部品の寿命を延ばすことで、メンテナンス頻度やコストを削減。
- 環境負荷の軽減:使い捨てや大量生産の回避につながる。
- 多様な用途への適応:基材や用途に合わせて材料を選択できるため、柔軟性が高い。
これらの特長により、多くの企業が溶射技術を導入し、製品の競争力向上を目指しています。
溶射のメリット
製品寿命の延長とコスト削減
溶射技術の最大のメリットは、製品の寿命を延ばし、維持管理にかかるコストを削減できる点です。溶射により製品表面が強化されることで、耐摩耗性や耐腐食性が大幅に向上し、使用環境の厳しい条件でも長期間使用可能となります。
例えば、製造業においては、生産ラインの部品に溶射を施すことで交換頻度が減り、ダウンタイムを最小限に抑えられます。これにより、生産効率が向上し、結果的に運用コストを削減できます。
具体例
自動車部品メーカーでは、エンジン部品に溶射を採用し、耐久性を高めることで、メンテナンスコストの削減に成功しています。
環境負荷軽減
溶射は、環境負荷を軽減する技術としても注目されています。 材料を必要な箇所にだけコーティングするプロセスは、材料の無駄を最小限に抑えます。 また、使用済み部品に溶射を施して再利用可能にするリサイクル技術としても利用されています。
さらに、溶射プロセスは比較的、低温で行われるため、従来の表面処理技術に比べてエネルギー消費が少なく、二酸化炭素排出量も抑えられます。
具体例
橋梁や建設設備に溶射を施すことで、長期的な環境負荷削減に寄与しています。
他の表面処理技術との比較(めっきや塗装など)
溶射は、めっきや塗装といった従来の表面処理技術と比べて、適用可能な基材や目的の幅広さで優れています。
例えば、めっきは液体溶液を使用するため、大きな基材への適用が難しい場合がありますが、溶射はその制約がなく、大型の基材にも均一にコーティング可能です。 また、溶射は非導電性材料にも適用可能であり、セラミックなどの特殊材料にも対応します。
一方、溶射のコストは初期投資としてやや高めですが、その長期的な耐久性と効率を考慮すると、トータルコストではむしろ経済的です。
技術 | 耐久性 | 基材の適用範囲 | 環境負荷 | 初期コスト |
---|---|---|---|---|
溶射 | 非常に高い | 広い | 低い | やや高い |
めっき | 中程度 | 制限あり | 中程度 | 低い |
溶射 | 中程度 | 広い | 中程度 | 低い |
溶射のデメリットと課題
初期コストや設備投資の負担
溶射技術を導入する際の最も大きな課題の一つが、初期コストや設備投資の負担です。 溶射に必要な機器や材料は高度なものが多く、導入時に高額な費用が発生する場合があります。 また、運用するための専門技術や人材の育成も必要であり、それに伴う教育コストも無視できません。
中小規模の企業では、特に初期投資へのハードルが高いと感じられることが多いです。 このため、溶射技術の活用を検討する際には、長期的なコスト削減効果や製品の寿命延長による利点をしっかりと見極める必要があります。
対応策
- 初期コストを分散するリースやサブスクリプション型サービスの活用。
- 専門業者に部分的なアウトソーシングを行い、コスト削減を図る。
技術的な制約と対応策
溶射技術には、いくつかの技術的な制約が存在します。
例えば、非常に薄いコーティングを必要とする場合や、複雑な形状の製品には適さない場合があります。 また、溶射材料の選択や加工条件によっては、コーティングの均一性に課題が生じることもあります。
これらの制約は、溶射の適用範囲を限定してしまう可能性があります。
さらに、厚膜成形が難しい場合や、大量生産には向かないとされるケースもあります。 特に、部品一つひとつの品質が厳密に求められる分野では、追加の加工が必要となることがあります。
対応策
- 最新技術を活用した高度なコーティング機器の導入。
- 使用する基材や形状に応じて、最適な溶射プロセスを選定。
- 代替的な表面処理技術(めっきや塗装)との併用を検討する。
溶射には上記のようなデメリットがありますが、これらを適切に対処することで、大きなメリットを享受できる可能性があります。初期コストの負担や技術的な制約をクリアできれば、企業にとって競争力を大幅に向上させる手段となるでしょう。
まとめ
溶射技術は、耐摩耗性や耐腐食性を高め、製品の寿命を延ばすだけでなく、環境負荷の軽減にも貢献する画期的な表面処理技術です。 その多様性と柔軟性は、製造業からインフラまで幅広い分野での活用を可能にしています。 特に、設備の維持管理コスト削減や持続可能な生産プロセスの実現といった、現代の企業が直面する課題を解決する強力な手段となるでしょう。
一方で、初期コストや技術的な制約といった課題も存在します。 しかし、リースやサブスクリプション型サービスの活用、最新技術の導入、適切な溶射プロセスの選定など、これらの課題に対応するための具体的な手段も整いつつあります。
溶射のメリットと課題を正しく理解し、自社のニーズや目標に合わせた適切な活用ができれば、製品の品質向上やコスト削減、環境保全に大きな効果をもたらします。 これからの時代、溶射技術は競争力を高めるための重要な選択肢となることは間違いありません。
溶射技術の詳細や導入を検討されている方は、ぜひ、当社の公式サイトをご覧ください。
https://www.koei-ts.co.jp/