記事公開日
溶接と切削加工の違いとは?種類と特徴、選び方のポイントを解説
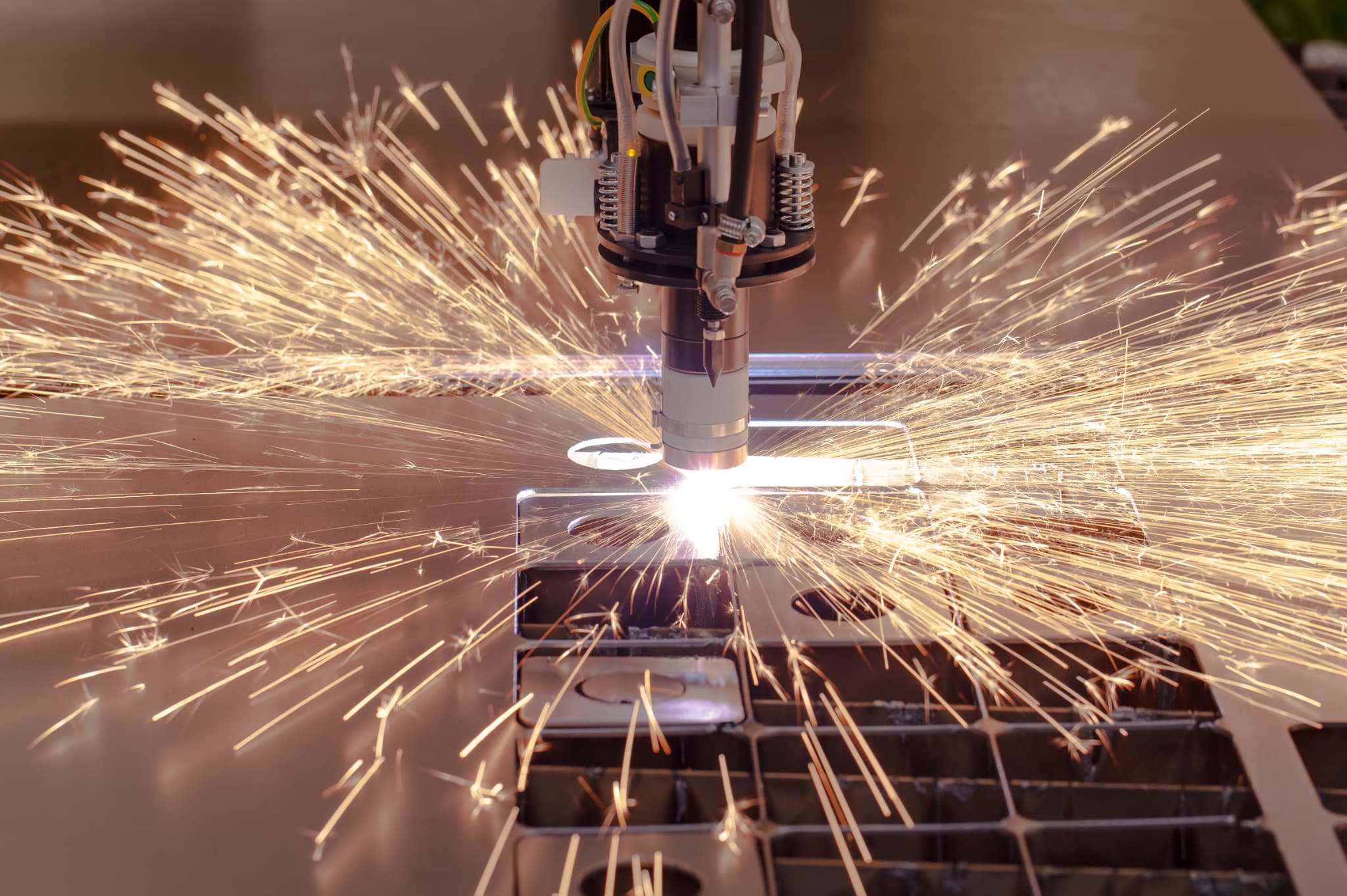
溶接と切削加工の違いは、金属加工に関わる業務やプロジェクトにおいて重要なテーマとなっています。これらの加工法には、それぞれ異なる特徴と用途があり、適切な選択が製品の品質や生産効率に大きな影響を与えます。
特に、日本の多くの企業や公共団体が、業務の効率化やコスト削減の観点から、この違いを正確に理解する必要性が高まっています。
本記事では、溶接と切削加工の基本的な違いを解説し、それぞれの種類や特徴、さらに用途に応じた選び方のポイントをご紹介します。
溶接とは?
溶接の特徴
溶接は、金属やその他の素材を接合するための加工方法で、主に熱や圧力を利用して部材を一体化させます。 高い強度と耐久性を持つ接合が可能で、産業分野において広く利用されています。
溶接は、建築、造船、自動車、航空宇宙など、さまざまな分野で活躍し、特に構造物の製造や修理に欠かせない技術です。
溶接の大きな特徴として以下が挙げられます。
- 高い接合強度:溶接部分は、適切な条件下で接合されると、母材とほぼ同等、もしくはそれ以上の強度を持つことが可能です。
- 多様な材料対応:金属だけでなく、プラスチックや複合材料など、幅広い素材の接合ができます。
- 設計の自由度:複雑な形状や大型構造物の製作が可能で、設計の幅が広がります。
一方で、溶接には課題も存在します。熟練した技術者が必要であり、作業環境によっては安全性の確保や設備の整備が求められます。
溶接の主な種類
溶接にはさまざまな種類があり、用途や素材に応じて適切な手法が選択されます。
以下に代表的な溶接方法を紹介します。
アーク溶接
アーク溶接は、電気アークを利用して高温を発生させ、金属を溶かして接合する方法です。 種類としては、手動アーク溶接(被覆アーク溶接)、TIG溶接、MIG溶接などがあります。これらは金属加工の現場で最も一般的に使用されています。
- メリット:多様な金属材料に対応可能。高い接合強度。
- デメリット:熟練した技術者が必要。溶接後の仕上げ作業が必要な場合がある。
レーザー溶接
高出力のレーザービームを使用して金属を溶接する方法です。 非常に高精度な溶接が可能で、電子機器や精密部品の製造に適しています。
- メリット:高精度、低歪み。狭い範囲での溶接が可能。
- デメリット:専用設備が必要でコストが高い。
抵抗溶接
金属部品を電流と圧力で加熱して接合する方法です。 点溶接やシーム溶接が代表的で、自動車部品の製造などに用いられます。
- メリット:自動化が容易で生産効率が高い。
- デメリット:接合部分が点や線に限定される場合がある。
フリクション(摩擦)溶接
接合面を摩擦によって発生する熱で溶かし、接合する方法です。 アルミニウムや異種金属の接合に適しており、航空宇宙や自動車産業で利用されています。
- メリット:異なる金属の接合が可能。接合強度が高い。
- デメリット:専用の設備が必要。
切削加工とは?
切削加工の特徴
切削加工とは、工具を用いて金属や他の材料を削り、希望の形状や寸法に仕上げる加工方法です。精密な仕上がりが求められる部品や製品の製造に最適で、多様な形状や寸法の加工が可能です。
切削加工は、製造業から建築、医療機器の製作など幅広い分野で使用されています。
切削加工の主な特徴は以下の通りです。
- 高い精度:微細な寸法調整が可能で、製品の寸法精度や仕上げの質が高い。
- 柔軟性:さまざまな形状や材料に対応可能。複雑な形状も工具を変えることで対応できます。
- 素材の活用:不要な部分を削るため、素材の無駄が少なくなります。
一方で、切削加工には課題もあります。たとえば、加工時間が比較的長いことや、大量生産には向かない場合があります。適切な工具の選定と加工条件の設定が重要です。
切削加工の主な種類
切削加工には、加工対象物や仕上がりの目的に応じた多くの種類があります。 ここでは、代表的な方法をいくつか紹介します。
旋盤加工
旋盤加工は、回転する素材を固定した刃物で削る方法です。 円柱状の部品や、シャフト類の加工に適しており、精密な寸法や形状の加工が可能です。
- メリット:効率的な加工。高い寸法精度を実現。
- デメリット:形状が回転対象に限られる。
フライス加工
フライス加工は、回転する工具で素材を削る方法で、平面や溝を加工するのに適しています。 形状の自由度が高く、複雑なパーツの加工にも対応できます。
- メリット:多様な形状加工が可能。精密な仕上げが可能。
- デメリット:加工時間が長い場合がある。
ボーリング加工
穴を広げたり形状を調整したりするための加工法です。 既存の穴を高精度に加工することが求められる場合に使用されます。
- メリット:精密な穴加工が可能。
- デメリット:専用の設備が必要な場合がある。
研削加工
研削加工は、研削砥石を用いて素材を削り、高い精度と滑らかな表面仕上げを実現します。 特に硬い素材の加工や表面仕上げに利用されます。
- メリット:滑らかな仕上がり、高い寸法精度。
- デメリット:加工速度が遅い。
ホブ加工
歯車やねじなどの特殊な形状を加工するための方法です。 工具が回転しながら素材に接触し、規則的な形状を作り出します。
- メリット:歯車やねじ加工に最適。
- デメリット:特定の形状に限定される。
溶接と切削加工を比較
溶接と切削加工は、それぞれ異なる特性を持つ金属加工方法であり、用途や目的に応じて選択されます。
以下では、加工精度、強度と耐久性、適用範囲や用途、コストや作業時間の観点から両者を比較します。
加工精度の違い
切削加工は、工具で素材を直接削るため、微細な寸法調整が可能です。そのため、精密部品や複雑な形状の製品を製作する際に優れています。 たとえば、自動車部品や医療機器のように高精度が求められる製品に適しています。
一方で、溶接は部材を接合することが主目的のため、加工後の寸法精度よりも接合強度が重視されます。接合部の仕上がりは作業者の熟練度や溶接方法に依存するため、切削加工と比較すると寸法精度は劣る場合があります。
強度と耐久性の違い
溶接は、溶融や圧力を用いて部材を一体化させるため、高い接合強度を実現します。 特に、建築構造や大型機械など、強度と耐久性が求められる製品で活躍します。 ただし、接合部が応力の集中点となる場合があり、設計や加工条件に注意が必要です。
切削加工は、部材全体を削り出すため、素材そのものの強度が保持されます。接合が必要ない一体成形のため、溶接のような接合部での強度低下がありません。 その結果、強度分布が均一で、高い耐久性が求められる精密部品で利用されます。
適用範囲や用途の違い
溶接は、異なる素材を接合する場合や、複雑な構造物を製作する際に適しています。 たとえば、橋梁、船舶、自動車のフレームなど、大型で複雑な構造物の製造に用いられます。 また、金属以外の材料(プラスチックや複合材など)を接合する特殊な溶接技術も存在します。
切削加工は、細部まで精密な加工が求められる部品や、滑らかな仕上がりが必要な場合に適しています。 たとえば、エンジンの部品や電子機器のハウジングの製造で使用されます。多様な形状やデザインを実現できる点が強みです。
コストや作業時間の比較
溶接は、熟練した作業者や特別な設備が必要な場合がありますが、大型構造物を短時間で接合できる効率性を持っています。 一方で、後処理(溶接ビードの研磨など)が必要な場合があり、追加の作業時間とコストが発生することがあります。
切削加工は、製造の精度が高い反面、素材を削る工程が多いため、加工時間が長くなる場合があります。 また、大量生産にはコスト効率が低くなる傾向があります。 ただし、CNC(コンピュータ数値制御)などの自動化技術を活用することで効率化が図れます。
溶接と切削加工の選び方
金属加工において、溶接と切削加工の選択は、製品の用途や要件、予算に大きく影響を与えます。 それぞれの加工法には特有の利点があるため、目的に応じた最適な選択を行うことが重要です。
以下では、選択のポイントを具体的に解説します。
用途に応じた選択のポイント
溶接と切削加工は、用途に応じて選択が異なります。
溶接は、構造物や大型機械の製造など、強度が必要で部材同士の一体化が重要な場面に適しています。 たとえば、建築物のフレームや船舶、自動車の車体製造などが代表例です。
一方、切削加工は、精密部品や細かい形状が求められる製品に適しています。 たとえば、エンジン部品、精密機器、医療用部品などです。
選択の際には、製品が求める機能性や耐久性に基づいて適切な加工方法を選ぶことが必要です。
加工対象の素材や製品の要求性能からの選択
素材や要求性能も加工方法を選ぶ際の重要な要素です。
素材の種類
溶接は金属同士を接合する際に有効で、特に鉄やアルミニウム、ステンレス鋼などの接合に利用されます。 一方で、異種材料の接合には特殊な技術が必要です。 切削加工は金属だけでなく、樹脂や複合素材などの幅広い材料に対応可能です。
製品の要求性能
溶接は、接合部の強度が重視される製品に適しています。 切削加工は、製品全体の均一な強度と高い寸法精度が求められる場合に選ばれます。
生産規模やコスト効率を考慮した選び方
製造コストや生産規模も重要な検討事項です。
溶接
初期設備投資が必要ですが、大量生産や大型構造物の製造においては高い効率を発揮します。
ただし、溶接後の後処理(たとえば、研磨や塗装)が必要な場合、追加コストが発生することがあります。
切削加工
高い精度が求められる少量生産やプロトタイプ製作に適しています。 CNC(コンピュータ数値制御)技術を活用することで、複雑な形状を自動で加工することができ、効率化が可能です。
ただし、削り出しに伴う素材のロスが発生するため、大量生産ではコスト効率が低下することがあります。
まとめ
溶接と切削加工は、金属加工の中でも特に重要な技術であり、それぞれが持つ特徴や利点を理解することで、製品の品質や生産効率を向上させることが可能です。
溶接は、部材を接合して高い強度を実現する加工法で、構造物や大型機械の製造に適しています。一方で、切削加工は、素材を削ることで高精度な仕上がりを実現する方法で、精密部品や複雑な形状が求められる製品に向いています。それぞれの加工法は、使用する素材、製品の要求性能、予算や生産規模によって適切に選択されるべきです。
また、溶接と切削加工を組み合わせることで、製品の設計や製造においてさらなる柔軟性と効率性を得ることも可能です。製品の要求に応じて、どちらの加工法を選ぶか、あるいは両方を活用するかを慎重に検討することが求められます。
最適な加工方法を選択することで、製品の競争力を高め、コスト削減や生産効率の向上を実現することができます。本記事が、溶接と切削加工の理解を深める一助となり、貴社の製造プロセス改善に役立つことを願っています。